Railroads
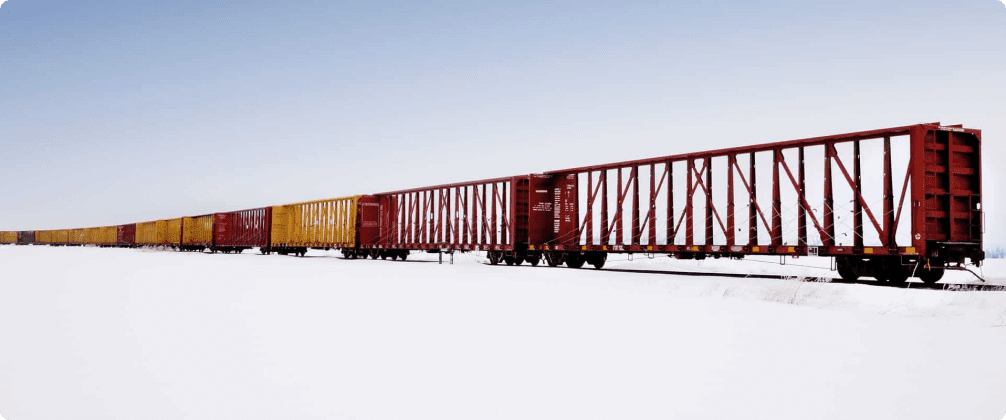
The Problem
Rail is usually replaced because of fatigue or wear — be it head wear in tangent track or gauge-face wear in curves. HAL tests show that wear, deformation, and fatigue-resistance are very strongly influenced by the hardness and metallurgical microstructure of rail steels. Standard carbon rail (especially when used in curves, turnouts and special trackwork features like frogs — featured in the photo above) is prone to stress cracking, wear and fatigue failure.
The cost of turnouts and special trackwork in railroad maintenance of way budgets explodes with the onset of heavy axle load freight traffic. That’s why so much research and development goes into improved designs, materials, and maintenance procedures to help these expensive items survive under HAL traffic. Just how expensive? Every year North American railroads spend over $1 billion in component replacements, maintenance, and train delays and derailment costs stemming from turnouts and other special trackwork. Costs for global railroad vendors would be comparable. The Duralife Process offers an exciting material improvement procedure to help contain some of the worst of these costs.
Impect Of The Problem
Under heavy loads special trackwork like crossing diamonds and turnout components (e.g., frogs), can incur severe damage. Early tests produced grim results. High impact components such as diamond crossings exhibited severe wear and/or deformation, required significantly more maintenance, and in some cases failed altogether.
Early tests of 315,000-pound cars produced track failures that could have shut down a main line or drained a MOW budget. Spot track maintenance needs increased 66 percent, and overall maintenance by about one-third.
Solving The Problem
Under heavy loads special trackwork like crossing diamonds and turnout components (e.g., frogs), can incur severe damage. Early tests produced grim results. High impact components such as diamond crossings exhibited severe wear and/or deformation, required significantly more maintenance, and in some cases failed altogether.
Early tests of 315,000-pound cars produced track failures that could have shut down a main line or drained a MOW budget. Spot track maintenance needs increased 66 percent, and overall maintenance by about one-third.
Cost Savings
In the U.S. nearly 700,000 tons of rail are replaced each year at a cost of about $400 million— one of the largest capital expenditures in the railroad industry. As rail costs skyrocket, extending its life becomes a matter of great importance. Research has already shown the use of clean steels increases rail life by a factor of five or more. Improved rail steels last 100-percent longer on tangent track and mild curves, and a 150-percent longer in moderate curves. At current traffic volumes, this increase in rail life represents savings of hundreds of millions of dollars per year (including installation costs) for US rail companies. Duralife processed rail, under the demanding conditions of HAL freight, could effectively double these results for overseas rail providers, resulting in savings of millions of dollars.
Beyond Rail
The wear from heavier cars can also be reduced by using premium steel in vehicle suspension components themselves. In HAL tests lateral forces dropped by 50 percent when premium steering trucks were used — which trebled track gauge-maintenance cycles on timber sleepers or ties. Wheel and rail surface damage also declined. Service tests showed a 50-percent reduction in flange wear and a 20-percent reduction in wheel tread wear under heavy axle loads. When Canadian Pacific adopted premium trucks for cars on some of its coal routes in western Canada, they generated improved curving, better wheel performance, reduced lateral forces and a 5.4-percent reduction in fuel costs,”said David Meyler, CPR’s general manager of mechanical services.
The microstructure of the rail components shown in the photo to the left are prime candidates for Duralife processing to yield improvements in wear resistance and stability.
Other Target Rail Markets
- Track laying machines
- Track measuring and testing equipment
- Rail drills and drilling equipment
- Rail benders
- Rail creep adjusters
- Track grinding or planing machines
- Rail cutting machinery and equipment
- Welding machinery and equipment
- Rail lifters
- Rail stretching equipment
- Notching and drilling machines for railway sleepers
- Ballast compacting machinesTrack laying machines
- Track measuring and testing equipment
- Ballast compacting machines

- Ballast clearing machines
- Ballast cleaning equipment
- Hand tools, plate layers spacers
- Light railway construction and maintenance machinery and equipment
- Trucks and workshop wagons for laying and repairing railway tracks
- Track grinding or planing machines
- Rail cutting machinery and equipment
- Snow clearing equipment
- Railway track cleaning vehicles
- Railway sleeper binding machines Installation equipment for overhead lines
- Maintenance and repair cars for railway overhead lines